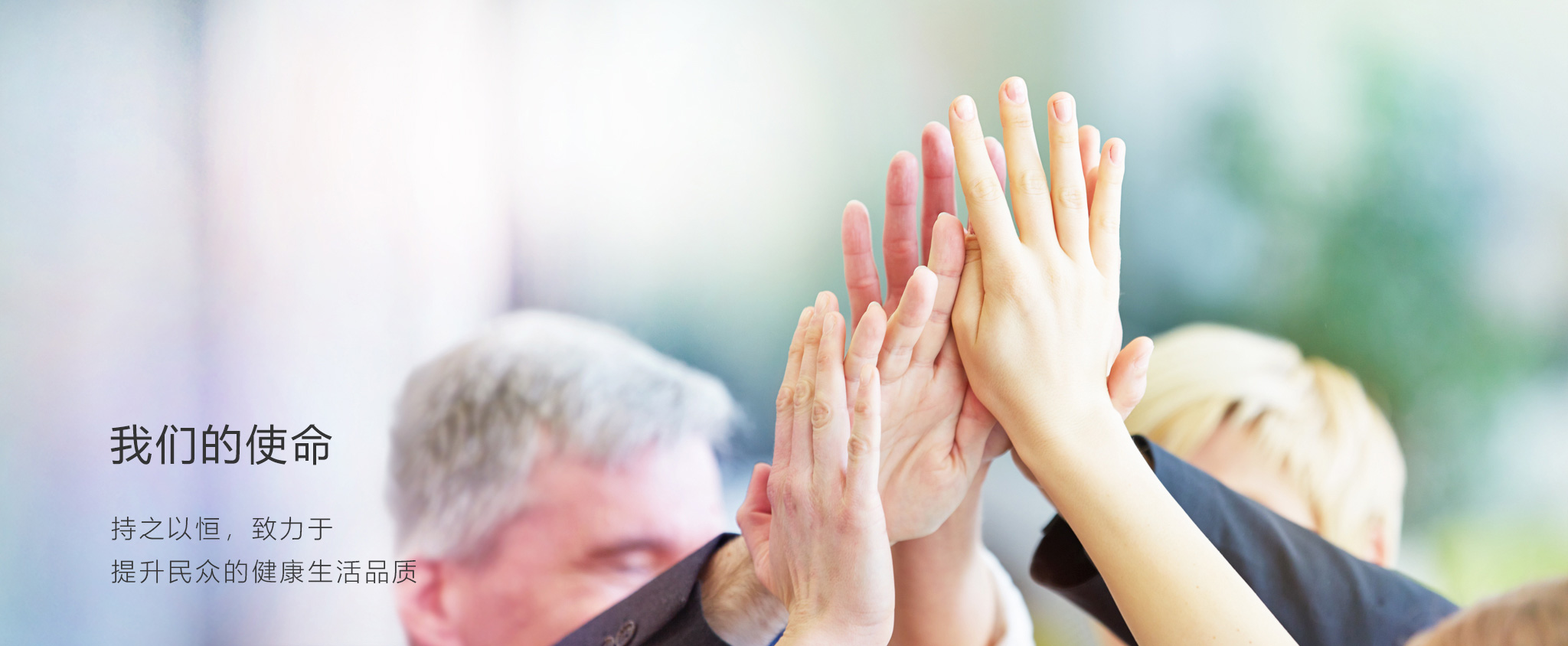
A级:高风险操作区域,如灌装区、防止胶塞桶和与无菌制剂直接接触的敞口包装容器的区域及无菌装配或连接操作的区域,应当用单向流操作台(罩)维持该区的环境状态。这种局部的洁净区可以使用洁净工作台、层流罩等设备。
洁净度的四个级别ABCD这种说法主要用于制药行业。ABCD的分级标准来自世界卫生组织(WHO)颁布的GMP,是制药行业通行的药品生产质量管理规范。2011年,中国新版的GMP(药品生产质量管理规范)施行,制药行业开始使用世卫组织的分级标准,用ABCD区分洁净区的级别。GMP四个等级 美国联邦209E标准。
高效过滤器检漏率大于997%,照度在300-600LX之间,噪声≤75db。B、C、D级洁净区的温度、湿度、换气次数、风速、照度和噪声标准与A级类似,但压差要求不同,B级相对室外压差≥10PA,C级和D级则分别为10PA。所有级别洁净区均需确保空气洁净度和环境参数稳定,以确保药品生产过程的无菌和质量控制。
这些区域通常通过层流操作台(或罩)来保持无菌环境,层流系统确保工作区的空气质量。 B级为无菌药品生产中非高风险操作区,可能包含某些无菌操作,但环境控制相对较宽松。 C级和D级分别用于生产非无菌药品和包装操作,环境控制标准相对更低。
新版GMP中的A、B、C、D级洁净区与百级、万级、十万级之间存在显著区别,它们在控制方式和标准上有所不同。A、B、C、D级洁净区区分了静态和动态条件,而百级、万级、十万级则主要基于静态标准。具体来说:A级代表动态百级,即在活动状态下仍需达到百级的清洁度,相当于ISO8级。
车间空气净化等级。30万级; 微生物最大允许数:1000 浮游菌/立方米;适用场合:丸剂、颗粒包装车间。10万级;微生物最大允许数:500浮游菌/立方米; 适用场合:注射剂浓配车间。1万级;微生物最大允许数:100浮游菌/立方米 ;适用场合:小容量注射剂灌装车间,直接接触药品的包装材料最终处理车间。
GMP药厂洁净车间的洁净度等级分为A、B、C、D四级,分别对应不同的生产区域和洁净要求。A级为最高洁净度级别,用于关键生产操作区;B级为背景区域;C级和D级则用作辅助区域。
gmp药厂洁净车间是为药品量身定制的特殊洁净车间,提供无尘、无菌的生产环境,防止污染,确保药品质量。根据药品和不同生产步骤要求,车间分为ABCD四个洁净度等级。A级重要操作区,B级为背景区,C级和D级为辅助区。车间根据药品工艺需求设置温度和湿度,对照度、噪音也有要求,人员穿着、操作严格。
按照GMP设计要求,药厂生产厂区通常分为一般生产区(无洁净要求)、控制区(100000级、300000级)、洁净区(10000级)和无菌区(100级)。药品是用来治病救人的,为保证药品的质量和安全,GMP规定,制剂生产、原料精烘袋、制剂使用的原辅材料、与药品直接接触的包装材料等,均应在洁净区内进行。
药厂可分为以下4个级别:A级:高风险操作区,如:灌装区、放置胶塞桶、敞口安瓿瓶、敞口西林瓶的区域及无菌装配或连接操作的区域。通常用层流操作台(罩)来维持该区的环境状态。层流系统在其工作区域必须均匀送风,风速为0.36-0.54m/s(指导值)。应有数据证明层流的状态并须验证。
可分为以下4个级别:A级 高风险操作区,如:灌装区、放置胶塞桶、敞口安瓿瓶、敞口西林瓶的区域及无菌装配或连接操作的区域。通常用层流操作台(罩)来维持该区的环境状态。层流系统在其工作区域必须均匀送风,风速为0.36-0.54m/s(指导值)。应有数据证明层流的状态并须验证。
1、在无尘车间十万级中,空气中的微粒和微生物数量被严格控制,以创造一个高度洁净的环境。这个级别的无尘车间的微粒浓度标准是每立方英尺空气中不得超过10万颗微粒。这比普通环境中的微粒浓度要低得多,因此能够大大降低产品受到微粒污染的风险。
2、避免对人和环境造成危害。在工作状态下能保持工作空间内的风速、空气洁净度、噪声、振动和照明等性能参数满足实验室使用的要求,广泛应用于生物实验室、医疗卫生、生物制药等相关行业,对改善工艺条件,保护操作者的身体健康 ,提高产品质量和成品率均有良好的成效。
3、无害,无尘车间是将空气中的微粒子、有害空气、细菌等污染物排除。目前已在电子光电、精密仪器、食品饮料、生物制药、医疗卫生、科研试验等领域普及应用。有百级、千级、万级、十万级,百级为最高等级。
4、制药业净化无尘车间一般以洁净度、CFU和GMP认证为标准,一定要保证室内洁净,不能交叉污染。
5、不同级别的洁净度对这些微生物的数量有严格限制。总的来说,洁净度标准旨在确保空气环境中的微粒和微生物含量在可控范围内,以满足特定领域的卫生和产品质量要求。这些等级的划分和参数是根据粒径大小和粒子数量来确定的,对于各种应用场景,如制药、电子、实验室等,都有着至关重要的指导作用。
6、空调设计、安装和运行应满足不同的目的,所以系统需要严格测试、控制和验证。制药工厂空气净化系统的主要用途是防止产品和洁净区受到微生物污染,防止用于制药生产的病毒、致病菌和芽孢菌的扩散和污染,防止诸如青霉素或其他高活性药品的扩散和污染,防止固体粉尘的扩散污染。
1、聚乙烯和聚丙烯两者均属于易燃品,在火灾危险危险等级中均属于严重危险级。聚乙烯:聚乙烯易燃,氧指数为14,燃烧时低烟,有少量熔融落滴,火焰上黄下蓝,有石蜡气味。聚乙烯容易光氧化、热氧化、臭氧分解,在紫外线作用下容易发生降解,炭黑对聚乙烯有优异的光屏蔽作用。
2、初效过滤器有板式、折叠式、袋式三种样式,板式是采用铝框加镀锌铁丝骨架加过滤棉的折叠式结构,有46MM和96MM两种厚度可供选择,过滤等级有G3,G4,符合防火分类标准DIN53438-F1和UL900-CLASS过滤器结构简单,安装方便,容尘量大,阻力低,性价比高,已与众多客户签订了长期合作伙伴关系,是您理想的选择。
3、药品仓库管理制度库内严禁烟火,非管理人员不准随便入库。库内应备有有效的消防器材,并按照学校有关的安全规定执行。各类药品库房根据药品性质采取有效的降温通风措施、各库房应备有温度计,注意观察室温,室温超出规定时要及时采取措施。不同的药品要分类存放管理。
4、可以有效起到防尘、防火花四处飞溅、防紫外线照射、防止人的眼睛在焊接过程中受到损害、防止火花飞到其他物体上引起燃烧等作用。
5、甲类仓库是一种用于存储特殊物品的仓库,通常用于存放具有较高火灾危险性的物品。由于其存储物品的特殊性质,甲类仓库在设计和建造上有着特殊的要求和规定。这种仓库必须符合一系列严格的安全标准,以保障人员和财产安全。下面将对甲类仓库进行详细解释。甲类仓库的主要特点是其高度的防火等级。
6、在FED-STD-2里面,无尘车间被定义为具备空气过滤、分配、优化、构造材料和装置的房间,其中特定的规则的操作程序以控制空气悬浮微粒浓度,从而达到适当的微粒洁净度级别。
1、洁净车间等级是根据空气中的微粒数量来划分的。不同级别的洁净车间适用于不同的行业和应用场景,例如,百级洁净车间通常用于高洁净要求的精密制造业。随着洁净等级的提高,车间内允许存在的微粒数量逐渐减少,对环境控制的要求也越高。这些洁净车间广泛应用于电子、制药、医疗、食品等行业。
2、洁净车间的等级一般是根据其内部环境的洁净程度来划分的。常见的洁净车间等级包括百级、千级、万级等。百级洁净车间是最高等级的洁净车间。具体划分标准和要求因行业标准不同而有所差异。
3、洁净车间的等级是根据灰尘颗粒大小和数量来确定的,在一定量的空气中所含微粒数量多的洁净度等级低,数量少的接近多等级高。
GMP D级:适用于包装区、办公区等非关键区域,空气洁净度要求为100,000级。GMP C级:针对制剂区等较关键区域,空气洁净度要求提升至10,000级。GMP B级:重要操作区域,如灌装区、分装区,空气洁净度要求为1,000级。
GMP洁净室按四个等级划分,A级区为高风险操作区,如无菌装配线,维持高洁净度状态。B级区为无菌配制和灌装区域的背景环境。C级和D级区分别为生产过程中重要程度较低的洁净操作区。A级对应动态百级,B级为静态百级,C级为万级,D级为十万级标准。
按照GMP设计要求,药厂生产厂区通常分为一般生产区(无洁净要求)、控制区(100000级、300000级)、洁净区(10000级)和无菌区(100级)。药品是用来治病救人的,为保证药品的质量和安全,GMP规定,制剂生产、原料精烘袋、制剂使用的原辅材料、与药品直接接触的包装材料等,均应在洁净区内进行。
洁净车间的级别五个等级分别是:百级、千级、万级、十万级和三十万级。洁净车间,也称为无尘车间或洁净室,其主要功能是控制一定空间内的空气洁净度。根据不同行业和洁净要求,洁净车间分为五个级别。
gmp车间洁净度等级标准如下:洁净操作区的空气温度应为18至26摄氏度。洁净操作区的空气相对湿度应为45%至60%。房间换气次数:大于等于15次每小时。压差:100,000级区相对室外大于等于10Pa。高效过滤器的检漏大于百分之997。照度:大于300lx-600lx。噪音:小于等于75db。
GMP十万级净化车间,是制药、食品等行业遵循严格的质量与卫生管理规范。它旨在创建一个无尘、无菌、易清洁的生产环境,确保产品安全。按照美国联邦标准,GMP净化车间分为100级、1000级、10000级和100000级,其中十万级是最低标准,对尘埃粒子数有明确规定。